Introduction
Material issue/receipt comprises issuing the raw materials to the supplier for making the finished or semi-finished product and receiving the finished products from the supplier.
The Material issue/receipt feature in RPOS7 helps to manage the stock of the raw materials and the finished products. User sends the raw materials to the supplier and maintains the stock details of the raw materials. The supplier receives the raw materials, makes the finished product and sends it back to the user. The user receives the finished product, fixes the selling price and updates the stock of the finished product. In this way, it helps the users to track the status of the inward finished products and at the same time manage the stocks of the products.
Example: Shirt is a finished product which requires cloth material, buttons, collar strips etc. as the raw materials.
In the material issue screen, user can enter the details of the raw materials issued for making the product. After receiving the finished product, the relevant entries are made in the material receipt screen. On making the material receipt, the stock of the issued materials is decreased and that of the finished products is increased.
Material Issue
Use the Material Issue screen to enter the raw material details issued to the supplier.
1. Click Inventory >> Material >> Material Issue. The Material Issue screen is displayed.
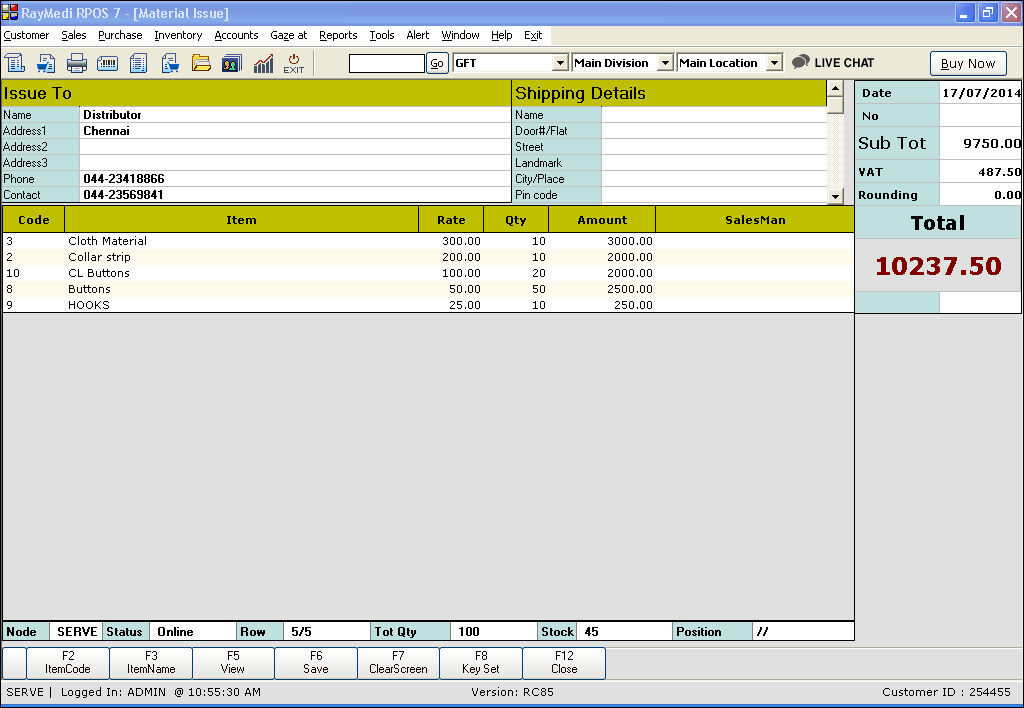
2. In the Issue To section, enter the details of the receiver to whom the material is issued.
3. In the Name field, press Enter. The Distributor LOV is displayed. Select the distributor. The details in the Issue To and Shipping Details are automatically loaded. The person to whom the items are issued i.e. the receiver name is created in the Distributor Master.
4. In the Item field, press Enter. The Item LOV is displayed. Select the items from the LOV.
5. In the Qty column, enter the quantity.
6. Click Save or press F6 to save the Material issue. After saving the Material issue entry, the stock of the raw materials gets reduced automatically.
Material Receipt
Use the Material Receipt screen to enter the details of the finished product received from the supplier.
1. Click Inventory >> Material >> Material Receipt. The Material Receipt screen is displayed.
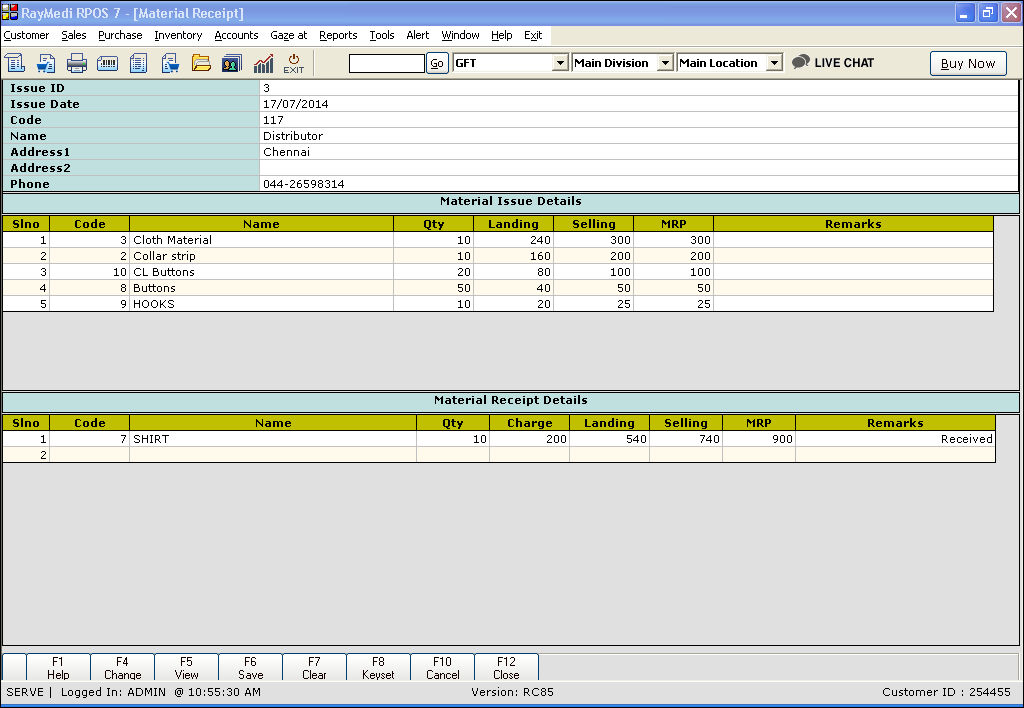
2. In the Issue ID field, press Enter. The material issue details LOV is displayed. Select the required issue details and it will be loaded in the screen.
3. In the Material Issue Details section, the details are automatically loaded.
4. In the Material Receipt Details section, enter the details as below.
- In the Code field, press Enter. The Item LOV is displayed. Select the item from the LOV.
- In the Qty field, enter the quantity of the items received.
- In the Charge field, enter the value for the making charges.
- In the Landing field, enter the landing cost for the item (finished product).
- In the Selling field, enter the selling price for the item.
- In the MRP field, enter the MRP for the item.
- In the Remarks field, enter comments if required.
5. Click Save or press F6 to save the Material receipt. After saving the Material Receipt, the stock of the finished product is increased.
For Reports: click here
For FAQs: click here